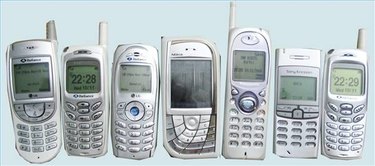
Various steps and processes are involved in the creation of a cell phone. Each cell-phone company may market a different style or model of phone, but the production of each one of those phones follows a similar trajectory. This article will provide a high-level overview of the making of a cell phone by a big manufacturing company, from design to quality control and delivery.
Step 1
Design a concept. Cell-phone companies employ a team of designers to create a concept for their latest phone release. They often try to surpass their previous model(s) by providing sleeker design and better functionality. The design concept goes through different stages, and the rendering of each part and functionality goes through a separate approval process.
Video of the Day
Step 2
Add and define features during the design phase. Features normally seen on a cell phone include the ability to make voice calls and send text messages; however, consumers can opt for additional features such as a built-in camera, video, MP3 player, Internet, GPS, instant messaging, games, radio, push-talk, playback recording, and anything you can think of that can fit into a small hand-held device.
Step 3
Identify parts to use, including the battery, hard case, keypad, volume control, Bluetooth enabler and wired headset socket, as well as the parts that make up the camera and MP3 player. Each cell phone consists of a microchip, like those produced by Broadcom or Qualcomm. The microchip, also called a SIM (Subscriber Identity Module) card, lets the cell phone work at high-speed standard known as W-CMDA.
Step 4
Build the parts after identifying them. Some parts are readily available from electronics makers like Samsung. Other distributors can deliver the small parts to a cell phone company's assembly line. During the building process, each part goes though rigorous quality control, to ensure that even the smallest part functions well.
Step 5
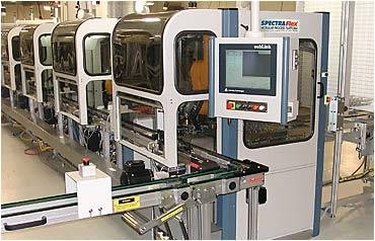
Put the cell-phone parts together. An assembly line consists of a row of multiple assembling machines to house the cell phones while they are being built. Because the small parts are sensitive to specks of material like and hair, people who operate the assembly machine wear clean coverall suits, complete with head covers. Furthermore, it is important to maintain the temperature in the room, to ensure that the machines do not break down due to overheating and the chips do not melt. Keeping the room between 55 and 65 degrees F is ideal.
Step 6
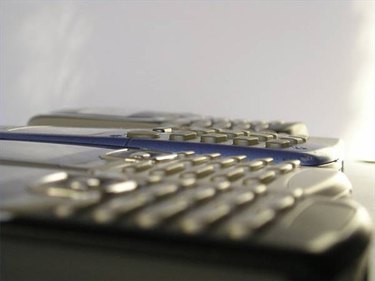
Test the phone in the QA (Quality Assurance) department before packaging. The QA analysts perform product testing for each functionality, as well as ascertaining the durability of the project. They test the signal, volume, battery power, key pads, screen resolution, photo, video, BlueTooth, texting, email, Internet and other features. If they find any problems, they will send the phone back for correction. Anything item does not pass the second time goes into the "reject" pile.
Step 7
Package all the systems that pass the QA Testing. After packaging, they are shipped and delivered.
Video of the Day